HSE RAPP (Risk assessment of pushing and pulling) の概要
(注意)
本資料は、HSEのRAPPについての文献[1] をもとに翻訳した内容を含む。
Copyright licenseの表記は以下の通りである:
This material contains public sector information published by the Health and Safety Executive and licensed under the Open Government License(この資料には、Health and Safety Executiveによって公開され、Open Government Licenseの下でライセンスされている公共部門の情報が含まれています)
HSEのサイト[3]では、HSEによる詳細な図入りの解説資料、動画マニュアル、オンラインソフトなどが公表されているので、最初はそちらを参考にすること(本サイトの図は、本サイト管理者作成の図です)。
その他、本資料では、表示の都合や日本の実態に合わせるため、表現を短めにしたり例示を置き換えたりした部分もある。使用に際しては、必ず原本の資料[1]をよく読んでおくこと。
手法の概要や入力項目についての説明は文献[1]に記載されているが、一部は文献[4]により詳しく説明されているので、そちらも参照すること。
【1】はじめに
HSEのRAPPツール(Risk assessment of pushing and pulling, 押し引きのリスクアセスメント)は、英国のHSE(Health and Safety Executive, 安全衛生庁)が開発した手作業による筋骨格系障害予防のためのアセスメントツール の1つである。台車を使った押し引き作業および台車を使用しない荷物の押し引き運搬のいずれかの作業を対象とする。
本法は、人間工学や産業保健の専門家ではない企業の雇用主や安全管理者の利用を想定している。取り扱い物や作業姿勢だけでなく、通路の状況や温熱環境などの作業環境も含めた広い要因のチェックと評価が可能である。
【2】使用方法
1.まず、評価対象場面を選定する。
・職場巡視で負担が高いと予想された場面
・作業者から負担が高いとの訴えがあった場面 など
2.各項目について、3~4段階で判定してスコアを決める。
各項目とも、緑・黄・赤及び紫の3~4段階に区分して判定する。各色の意味は以下の通り:
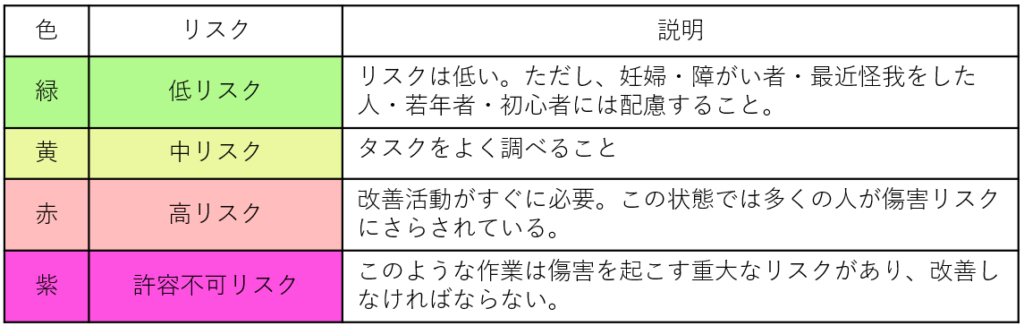
(注)本資料では、リスクの色を、緑(低リスク)・黄(中程度のリスク)・赤(高リスク)・紫(許容不可能なリスク)で示している。原法では、黄はAmbar(琥珀色,略記A)が使用されている。本資料では、日本国内の通常の信号機の色区分にあわせて単純に「黄」(Yellow)と表記した。
3.項目ごとにリスクの色に応じたスコア(点数)が付く。
・各項目のスコアの合計点を求める。
・合計点が、リスクへのばく露の程度を示す値である。
4.リスクの判定色と合計点に応じて改善を行う。
・各項目の判定色のうち、緑以外の項目がある場合はそれを優先的に改善する。
・評価点の合計点を可能な限り減らすように改善する。特にスコアの高い項目を優先的に改善する。項目のうち、1や2など先に記載されている項目はスコアが高いので、これを優先的に改善するとよい。
【3】RAPP-台車押し引き-
台車に物を載せて手で押し引きして運搬する作業の評価法である。
台車は以下の3種類が想定されている:
- 台車小:一輪車や2輪車など、動かすのに常に手で支える必要があるもの
- 台車中:車輪が3個以上の台車やユーロビン(Eurobin)など、押すだけで動かせるもの
- 台車大:ハンドリフト・ハンドパレットなどと呼ばれるもの
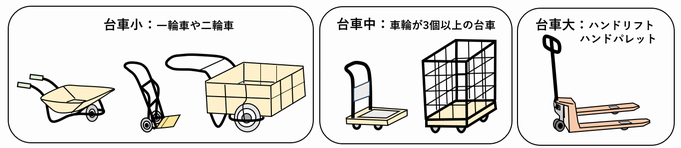
1.入力項目
以下の9項目である。
1)荷重
台車に詰む荷物の質量と台車の種類で区分する。ここでの荷重は、実際の押し引き力ではなく、台車と荷物の総質量である。
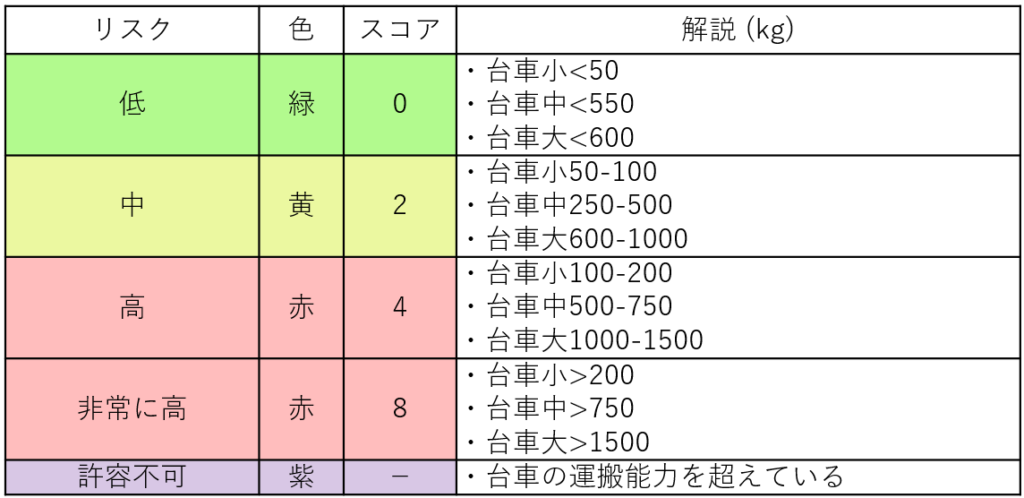
2)姿勢
台車を押し引きする際、強く前傾した姿勢で高い押し力を出さなければならない場合は、リスクが高い区分になる。
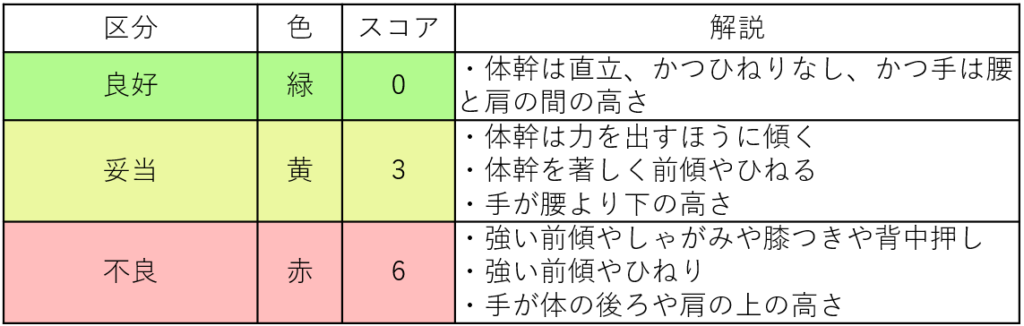
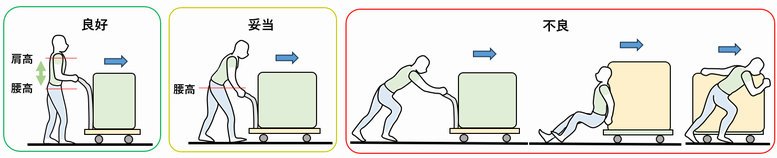
3)手の握り
持ちやすいかどうかである。
つかむ場所がないとか手が触れる部位に凹凸があって把持したり手をかけたりしにくい場合は、リスクが高いとみなす。
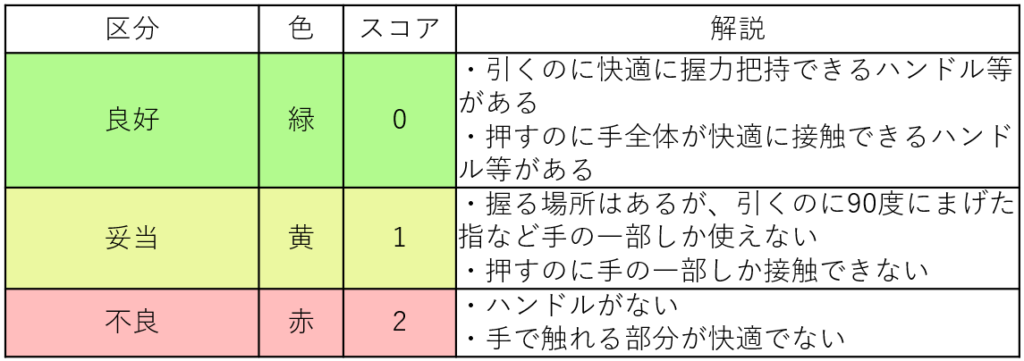
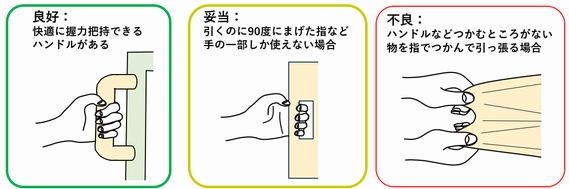
4)作業パターン
反復作業かどうかと、休憩や交代の自由度があるかどうかを評価する。
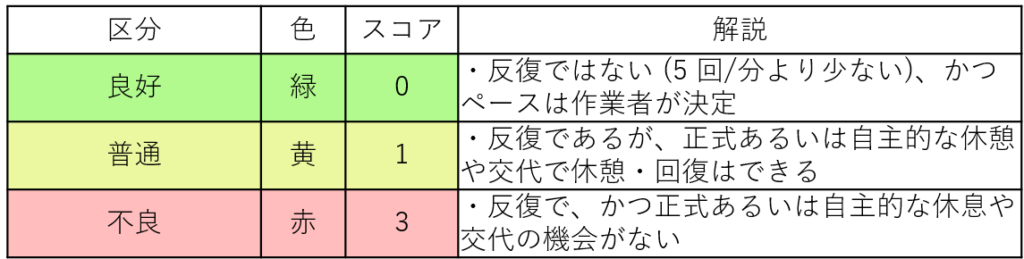
5)運搬距離
10 m以下の短い距離から30 m以上の遠い距離までを区分して入力する。

(補足)Liberty-MutualのLM-MMHの運搬では最大10 m、ISO 11228-1の運搬では最大20 mまでとなっている。それより長い距離の運搬はしなくて済むよう、設備レイアウト等を工夫する。
6)台車等の状態
台車も道具なので、定期的な保守が必須である。
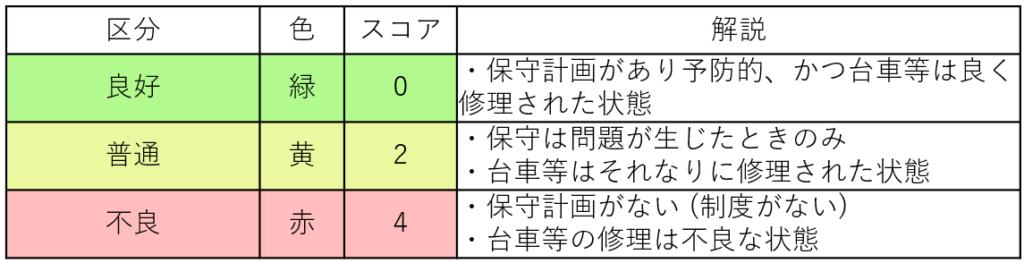
(補足)キャスターが壊れた台車は、押し力が高くなりかつ直進性も劣ってくるので事故の原因にもなる。かごの部分などが破損したままで使用すると、荷物の積み下ろしの際のけがの原因になる
7)床面
作業する場所の床面が滑りやすいとかぬかるむとかがれきがあるなどの制限があると、適切な位置に立って安定した持ち上げ作業ができなくなることに配慮した項目である。
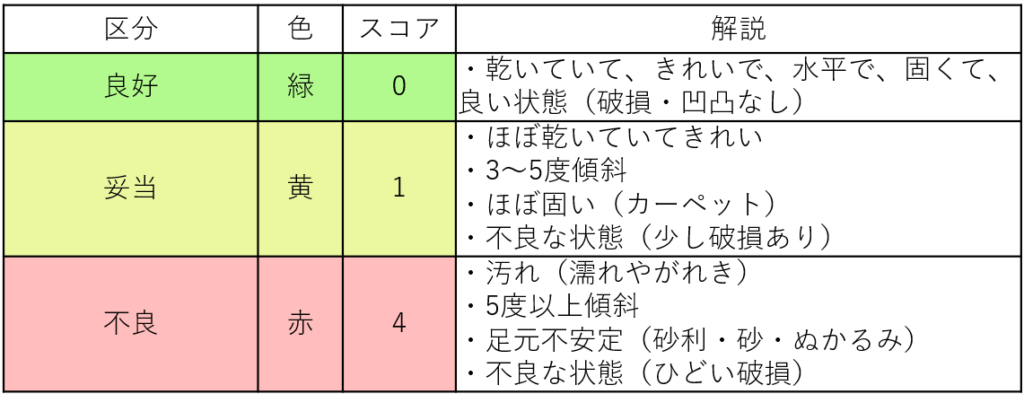
(補足)床面の凹凸やごみなどがある場所は、台車の押し引き力が突発的に変化して操作に負担になるだけでなく、事故の原因にもなりやすい。
8)運搬路の障害
閉じたドアや狭いドア、障害物の迂回、傾斜、はしごの使用などが考慮される。
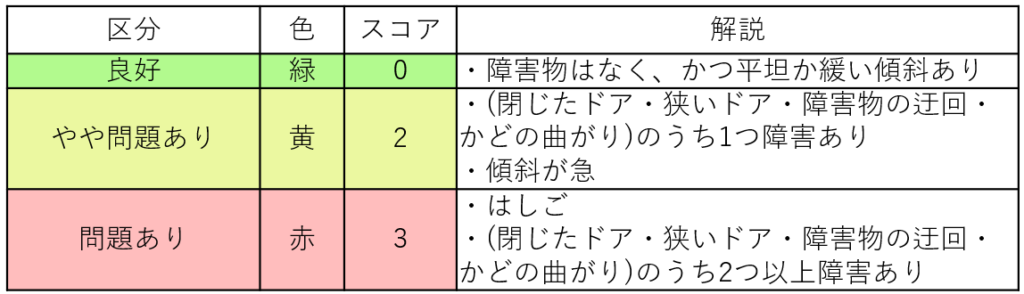
9)他の要因
荷物が不安定である、荷物が大きくて進路方向の視野がさえぎられるなど多様な項目が含まれている。それらが1つあるいは2つ以上あれば黄または赤になる。

他の要因の例
・設備や荷物が不安定
・荷物が大きくて作業者が移動する
・視野がさえぎられる
・設備や荷物がとがっていたり熱くて触れるとケガする可能性あり
・照明が不良
・暑すぎたり寒すぎたり、湿度が高すぎる
・突風や強い気流がある
・保護具や服のために設備が使いにくい
2.入力項目の取りまとめ
1~9の結果は以下の表にまとめておくとよい。各項目の判定色に〇をして、そのスコアを右欄に転記する。最後に各色の件数とスコアの合計を記載する。
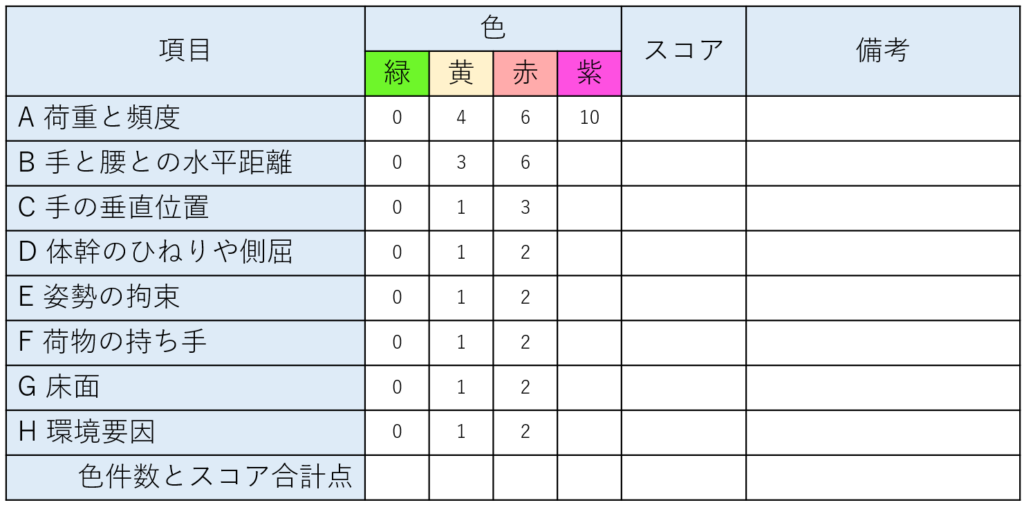
【4】RAPP-荷物押し引き-
車輪の付いた台車を使わず、転がしたり押し引きしたりして荷物を運搬する方法である。本法での運搬方法は以下の3種類である。
・丸い荷物を真横にしてころころ転がしながら押し運ぶ方法(「転がし」と仮称。 原文ではrolling)
・四角い荷物を傾けて荷物のかどを軸にして回転させたり底辺が丸い荷物なら少しだけ傾けて転がしたりしながら運ぶ方法(「斜め転がし」と仮称。原文ではchurning)
・荷物をそのまま引きずったり紐を荷物にかけて紐を引いて運んだりする方法(「引きずり」。原文ではdragging, hauling, sliding)
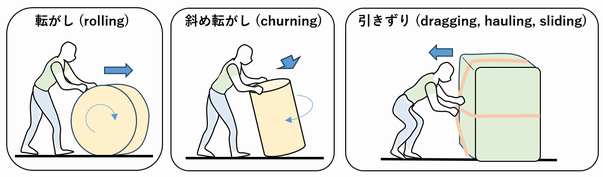
1.入力項目
以下の8項目である。
1)荷重
上記の3種類の押し引きの運搬方法ごとに、取り扱い物の荷重(質量)が示されている。
「引きずり」では、押し引きに必要な力が最も高くなるので、軽い荷重で高いリスクがあるように区分されている。
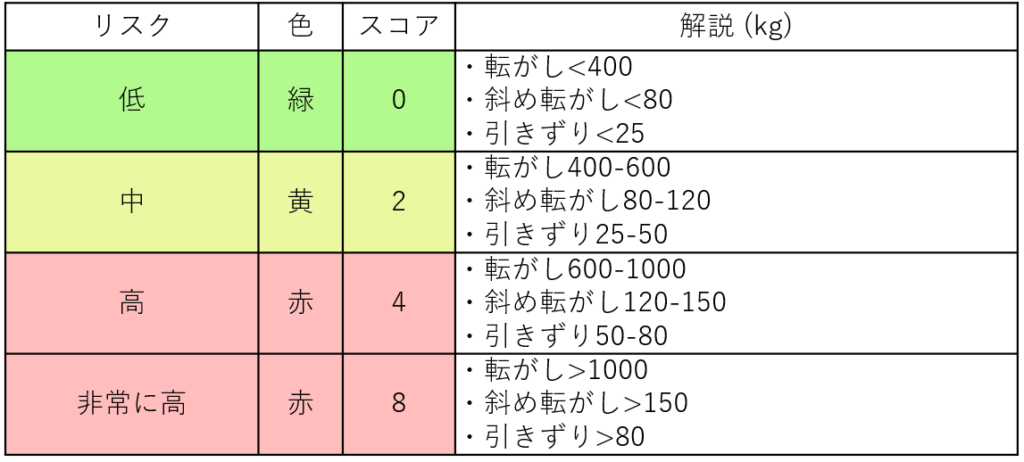
2)姿勢
押し引きをする際、体を前傾させて高い押し力を発揮しなければならない場合は、転倒しやすくリスクが高い。不良と区分される押し方だと、前方確認も操作力の制御も難しいので特にリスクが高い。
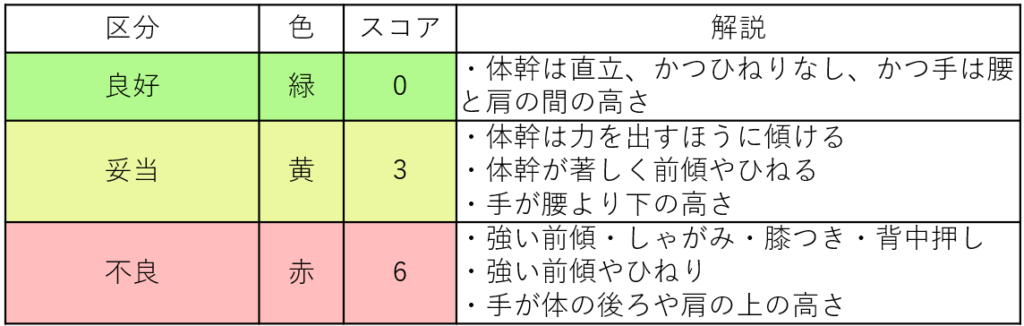
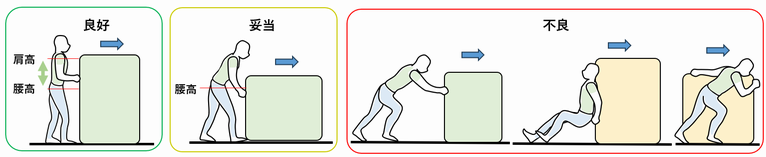
3)手の握り
持ちやすいかどうかである。
つかむ場所がないとか手が触れる部位の凹凸が激しくて把持したり手をかけたりしにくい場合は、リスクが高いとみなす。
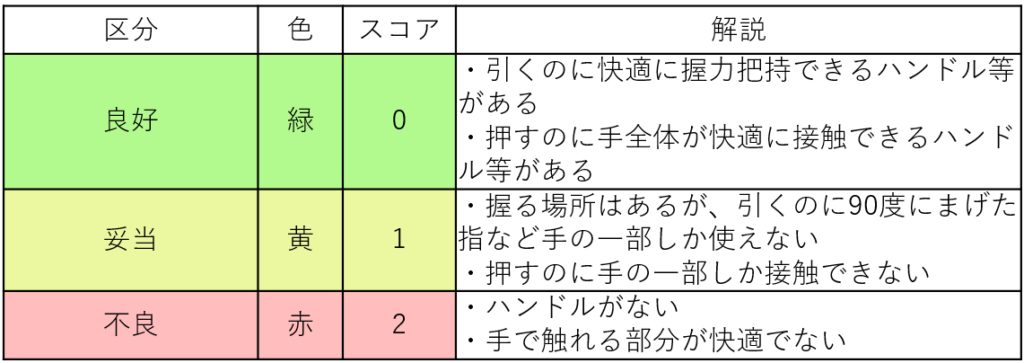
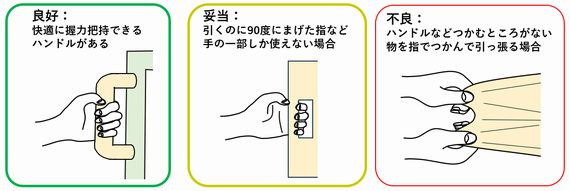
4)作業パターン
反復作業かどうかと、休憩や交代の自由度があるかどうかを評価する。
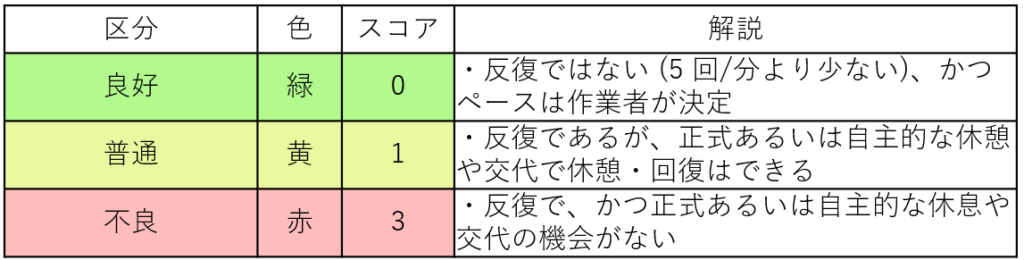
5)運搬距離
2 m以下の短い距離から10 m以上の遠い距離までを区分して入力する。
台車押し引きよりも短い運搬距離で高いリスクになるよう区分されている。

(補足)通常このような運搬法は、狭くて台車が入らないような場所や一時的な荷物の運搬場面で行われることが多い。一時的な作業法のつもりが、そのままに改善されずに続くことのないように注意する。
6)床面
作業する場所の床面が滑りやすいとかぬかるむとかがれきがあるなどの制限があると、適切な位置に立って安定した持ち上げ作業ができなくなることに配慮した項目である。
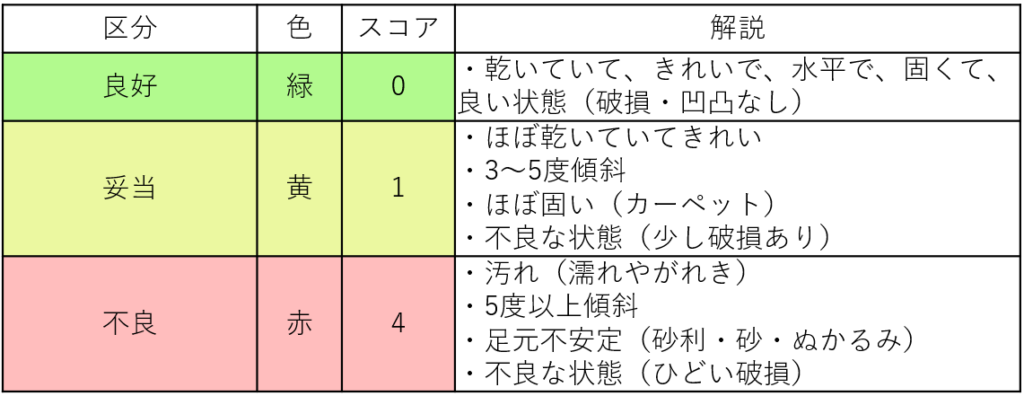
7)運搬路の障害
閉じたドアや狭いドア、障害物の迂回、傾斜、はしごの使用などが考慮される。
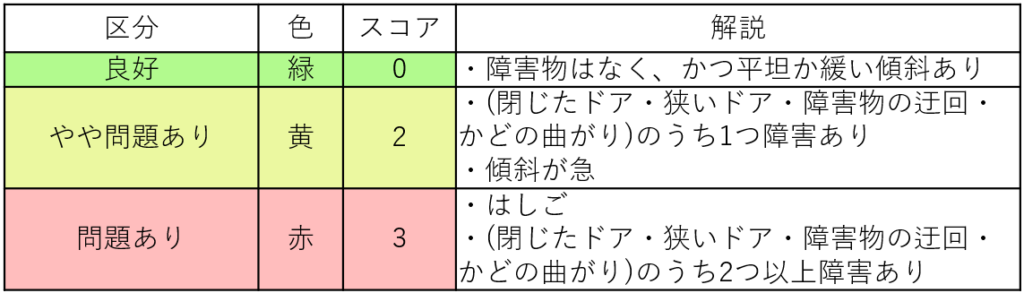
8)他の要因
荷物が不安定である、荷物が大きくて進路方向の視野がさえぎられるなど多様な項目が含まれている。それらが1つあるいは2つ以上あれば黄または赤になる。

他の要因の例
・設備や荷物が不安定
・荷物が大きくて作業者が移動する視野がさえぎられる
・設備や荷物がとがっていたり熱くて触れるとケガする可能性あり
・照明が不良
・熱すぎたり寒すぎたり、湿度が高すぎたりする
・突風や強い気流がある
・保護具や服のために設備が使いにくい
2.入力項目の取りまとめ
1~8の結果は以下の表にまとめておくとよい。各項目の判定色に〇をして、そのスコアを右欄に転記する。最後に各色の件数とスコアの合計を記載する。
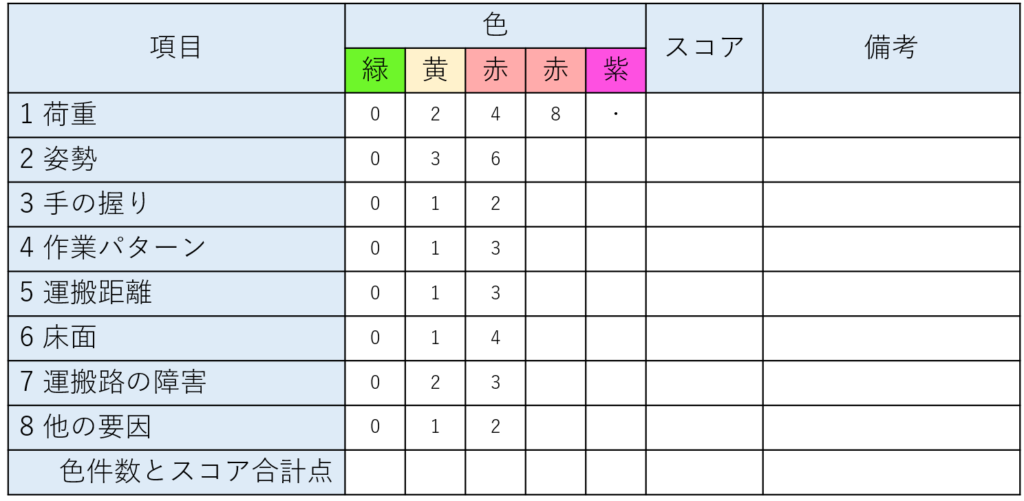
文献[1]~[3]にあるように、いずれの手法も原文では最後にまとめ用のスコアシートがある。必ず事前に確認のこと。
【5】まとめ
台車による運搬は、手のみでの運搬よりはるかに重い荷物を遠くまで繰り返し運ぶことができる。その分、適切に管理しないと、衝突や挟まれの事故の原因になりやすい。
同じ場所で作業する荷物持ち上げに比べ、運搬での通路は作業場として認知されにくく、状況も変化しやすくて管理が難しい。台車だけでなく、運搬通路の点検も欠かさぬようにすること。
文献
[1] Health and Safety Executive, Risk assessment of pushing and pulling (RAPP) tool, INDG478, 2016:RAPP toolのHSEのオフィシャルな解説書
[2] Health and Safety Executive, Manual handling assessment chars (the MAC tool), INDG383 (rev3), 2018.11:MAC toolのHSEのオフィシャルな解説書
[3] Health and Safety Executive, Manual handling at work, https://www.hse.gov.uk/msd/manual-handling/index.htm (2023/08/17閲覧)
[4] Health and Safety Executive, Manual handling -Manual Handling Operations Regulations 1992, Guidance on Regulations, L23 (Fourth edition), 2016:3手法を含む荷物取り扱い全般の規則1992(L23)の解説資料。